Leader in the textile industry
With the acquisition in 2013 of U.T.I.T., a world leader in automation for the Textile Industry, Trascar consolidated its leadership in the sector, also leading to the creation of a dedicated business unit in 2015.
Trascar can supply shuttle transport systems and spool transport systems (palletising, packaging, and automated warehouses).
Of the intermediate products, the roving bobbin is the most delicate to handle and it is precisely to preserve the quality of the Client’s product that Trascar offers an automated transport system from the bench to the spinning area through a system that flows in the corridors between the spinning machines and interfaces with the benches that feed the circuit with full roving bobbins. The level of automation of shuttle transport systems can be adapted to the specific needs of the client (from manual to fully automated).
The roving tube cleaner is an integrated system in roving bobbin transport. During cleaning, the tube is removed from the bobbin holder to make for high rotation speed, preventing wear on the roving bobbin holder. Thanks to the system designed by Trascar, in fact, the fibres open during the cleaning cycle allowing the machine to eliminate any fibre residues.
Lastly, the blower ensures continuous blowing and suction for optimal and continuous cleaning of all textile machines; this makes for threads that are always regular and clean, synonymous with high product quality.
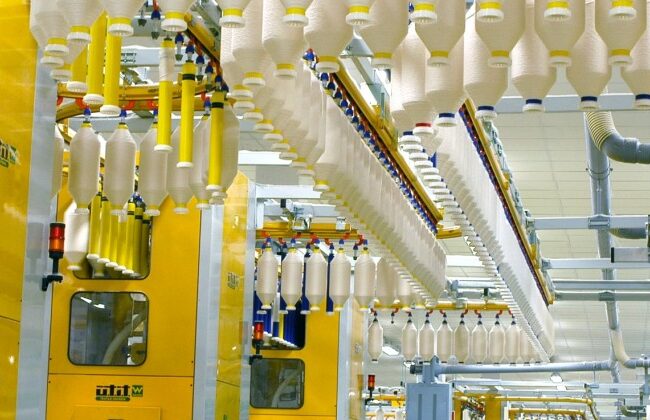
A decisive turning point in the automation process of a spinning mill
The installation of a spool handling system (automation of collection and palletising) represents a decisive turning point in the automation process of a spinning mill. The automation interfaces with the production line and takes care of the handling and packaging of the spools in a completely autonomous manner. The solutions offered by Trascar in the design stage let the client monitor the production cycle and the product in stock in real time; they also significantly reduce labour and production downtime costs.
The centralised palletiser is equipped with various palletising stations. The number and size of the stations are chosen based on the products processed or the number of production machines. Direct palletising offers the possibility to form the pallet according to the textile production machines, such as winders, open-end, vortex, etc. The palletising system is completed by the pallet packaging line, which automatically wraps, weighs, and labels the package.
The use of AGV trolleys makes it possible to manage pallet sorting between the various production/storage areas in a completely automatic way without the use of personnel. The extreme flexibility of the automated guidance systems used allows the execution of the most complex cycles.
With an automated pallet warehouse, it is also possible to optimise warehouse space; Trascar has built numerous automated warehouses for the various storage needs of its clients.
Designed by Trascar, the Automatic Transfer LTX8 machine for handling laps picks up the laps coming out of the lap formers and places them on the rear deposits of the comber machines that are do not have spare laps.
Eight (8) laps are transferred at the same time. The order of priority is due to the timing of the warehouse being emptied.
The Transfer LTX 8 automatically picks up the empty tube from the combers for its return to the originating lap former.