Since 1980, Manometal, based in Egna in the heart of South Tyrol, has been one of Italy’s leading companies in the turning industry.
The entire production, over 45,000,000 pieces per year, is monitored using the latest SPC technology, with the goal of delivering defect-free products to customers through continuous process capability control.
Manometal provides high-quality products while complying with legal and binding requirements and continuously improving its performance in terms of quality, environmental standards, and workplace safety. The company is singularly focused on consistently enhancing customer satisfaction.
Due to continuous growth, Manometal recognized the need to expand its logistics warehouse. After an open tender in collaboration with a consulting firm, Manometal selected Trascar as its partner for this significant new investment.
“We had purchased a new building because we needed more space and felt the need to better organize the different phases of our work. However, we needed to find a partner capable of setting up a new automated warehouse within a building that had significant structural constraints. This was something completely new and complex for us, which is why we turned to a consulting firm and launched a tender.
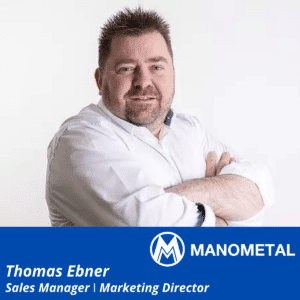
A CHALLENGING PROJECT
Within a pre-existing building originally designed to be a shopping mall, Manometal’s new automated warehouse had to be built.
The building posed structural limitations due to the pre-established floors, walls, and cavities. After a thorough internal analysis, a finished product automated pallet warehouse was installed, along with a picking bay for order preparation and a gantry system for storing bins exiting production.
All the technologies and internal movements were connected by conveyors designed to eliminate all strenuous activities for staff and automate processes.
The dedicated pallet stacker crane was the cornerstone of the project, allowing the optimization of the existing space thanks to its double-deep storage on one side and triple-deep storage on the other. Also noteworthy is the gantry system for storing finished product bins and managing the storage process. Due to the building’s limitations, all these operations are carried out on a newly built mezzanine with a weight limit per square meter. The gantry system autonomously defines the maximum load limit, providing, in addition to automated performance, a real guarantee of safety.
“Thanks to Trascar, we’ve achieved our goals: more space for our products and work, and a level of automation that can be summed up in two outcomes: the complete elimination of strenuous tasks for our employees—just consider that only women now work at our end-of-line stations—and perfect product traceability, from production to storage to delivery to our customers. For clarity, before the Trascar implementation, our staff had to manually handle bins weighing up to 15 kilograms multiple times per shift. That no longer happens, greatly improving everyone’s health and workplace safety. As for warehouse performance, we’ve always operated with the FIFO logic—first in, first out—and today, thanks to the innovation we’ve introduced with a partner like Trascar, FIFO is now our strongest asset. I would like to conclude by thanking the Trascar team, as they have supported us with seriousness and professionalism from the very beginning.”
Added Thomas Ebner, Sales Manager and Marketing Director of Manometal.
Given the continuous changes and improvements to Manometal’s production processes, after the project’s launch, the company engaged Trascar in a fine-tuning operation, incorporating specific customizations to optimize their evolving needs. Today, just over a year after its implementation, Manometal proudly declares itself an extremely satisfied customer.
“It was a challenging project, but thanks to the synergy between all departments, we achieved the excellent result desired by both the client and us.”
Concluded Matteo Ranuccini, Sales Manager of Trascar SpA.