Palletisers and De-palletisers, our solutions
Trascar supplies companies operating in various industrial sectors with palletising and de-palletising systems tailored to your company’s production needs. Depending on the sector and the type of product to be handled, our competent staff can offer you the best machines for robotic palletising of packaging, warehouse or production, highly customised solutions to maximise the productivity of your company without compromising on safety.
The automated palletising systems created by Trascar are cutting-edge solutions designed to speed up and optimise the production process of companies operating in any commercial and industrial sector thanks to the use of Cartesian and anthropomorphic robots with 5 or 6 controlled axes.
Bags, cartons, boxes, spools, and other types of products are sorted and transported to their destination through specific gripping devices using the EasyPallet software and the most suitable technologies for impeccable process management.
Call us or fill out the dedicated form to request more information.
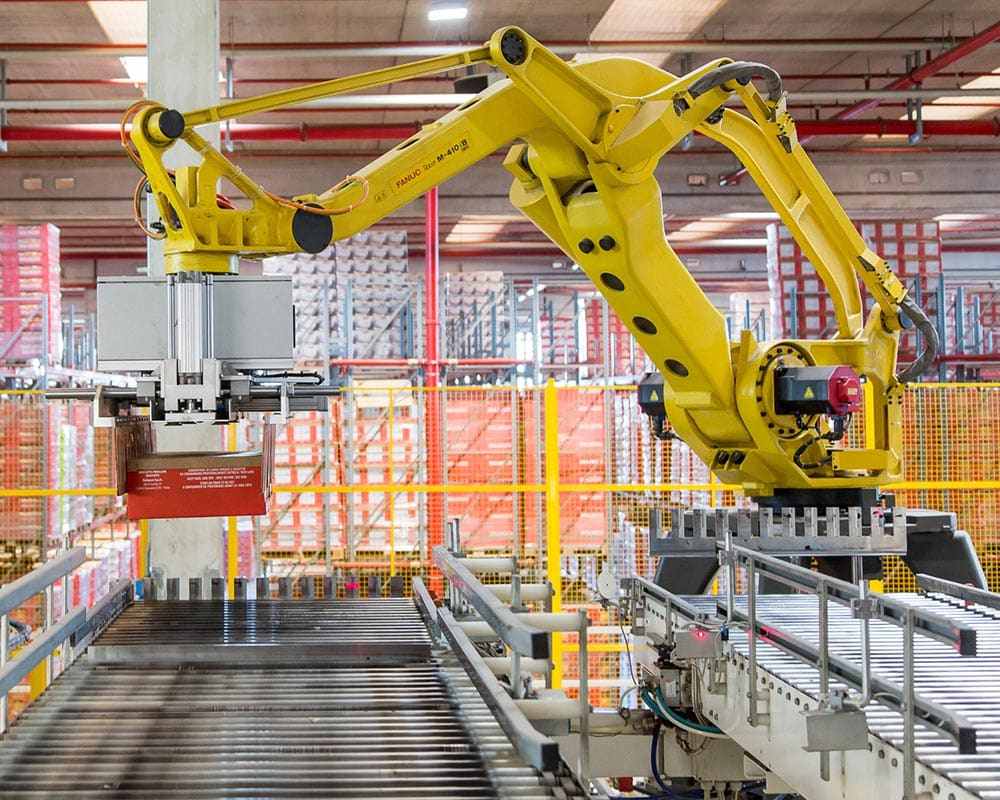
BUNDLES
FIND OUT MOREBUNDLES
Robotic palletising systems for bundles allow for the handling, compaction, stopping, and destination placement on the pallet in an efficient and orderly manner.
BOXES
FIND OUT MOREBOXES
We supply automated palletising islands for handling and arranging boxes on pallets, customisable solutions for different production lines.
CARTONS
FIND OUT MORECARTONS
We have palletising and de-palletising lines for cartons of different types and sizes equipped with ergonomic gripping devices depending on the product to be handled.
CRATES
FIND OUT MORECRATES
Custom palletisers and de-palletisers tailored to your company’s production needs to manage the handling and sorting process of crates effectively.
REELS
FIND OUT MOREREELS
We guarantee the best technologies for robotic palletising of film reels, Cartesian and anthropomorphic multi-axis-controlled solutions for optimal performance.
YARN SPOOLS
FIND OUT MOREYARN SPOOLS
We supply machines for the automated palletising and de-palletising of yarn spools, custom-made systems for handling and sorting on pallets of different sizes.
Our technologies at the service of your business
Investing in a palletising and de-palletising system means investing in the future of your business: with the use of cutting-edge technologies, you will achieve a substantial increase in company production, significant savings of time for storage and preparation operations of the final product, and total safety in all phases of the production process.
Choose Trascar to rediscover and enhance the core business of your company: contact us without obligation for a personalised consultation! We operate throughout Italy with companies operating in the industry of multiple sectors.