“Since way back in 1980, Manometal, based in Egna in the heart of South Tyrol, has been one of Italy’s top players in the turning industry.
Their whole production—over 45 million pieces a year—is kept in check with the latest SPC tech, making sure everything they ship out is totally defect-free, thanks to constant process monitoring.
Manometal pumps out high-quality products while sticking to all the legal and binding rules, always leveling up their game when it comes to quality, environmental standards, and workplace safety. The company’s laser-focused on keeping their customers happy, no doubt about it.
As the company kept growing, Manometal realized they needed to step up their warehouse game, too. After an open tender in partnership with a consulting firm, they picked Trascar as their go-to partner for this big new investment.”
“We quickly realized that the project was extremely challenging due to the space, our specific requirements, and especially the timeline. Everything had to be completed by June 30, 2023, to meet the deadlines required to obtain Industry 4.0 funding. Trascar immediately proved to be proactive and, thanks to its technologies, was able to bring our project to life. We started working together closely, and soon after, we signed the contract. Though I must admit, just a handshake with Giuseppe Gelati, CEO of Trascar, had already reassured and convinced me.”
That’s what Thomas Ebner, Sales Manager and Marketing Director at Manometal, had to say.
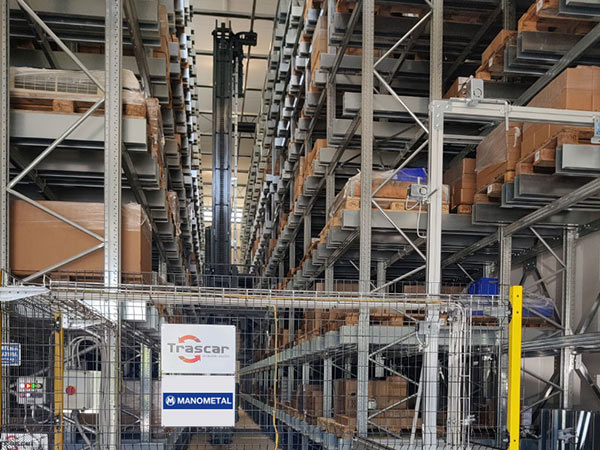
A TOUGH PROJECT
Manometal had to set up a new automated warehouse inside an old building that was originally meant to be a shopping mall.
The place had some serious limitations with its floors, walls, and pre-existing gaps. But after some solid planning, they managed to fit in an automated finished product pallet warehouse. They even added a picking bay to prep orders and a gantry system to handle bins coming out of production.
All the tech and movements inside were hooked up to conveyors that pretty much took care of all the heavy lifting, making life way easier for the workers.
The pallet stacker crane was a total game-changer for the project. It helped max out the space by allowing double-depth storage on one side and triple-depth on the other. The gantry system for storing finished product bins? Also a standout. Given the building’s limits, everything had to be done on a newly built mezzanine with a max load limit per square meter. The gantry, running on its own, figures out the max load limit, offering not just top-notch automation but serious safety, too.
“Thanks to Trascar, we’ve hit our goals: more space for our products and work, plus automation that’s a win-win in two ways—no more heavy lifting for our team (FYI, the folks working our end-of-line stations now are all women), and flawless product traceability from production to storage to shipping. To give you an idea, before Trascar came in, our crew had to lift bins weighing up to 33 pounds, multiple times per shift. Now? That’s a thing of the past, which is awesome for everyone’s health and safety. And when it comes to the warehouse, we’ve always followed FIFO—first in, first out—and now, thanks to all the innovation Trascar brought, FIFO is our secret weapon. Big shoutout to the Trascar team; they’ve been with us every step of the way, showing real professionalism.”
That’s from Thomas Ebner, Sales Manager and Marketing Director at Manometal.
Since Manometal’s production processes are always evolving, after everything was up and running, they called Trascar back for some fine-tuning—custom tweaks to keep everything running smoothly with their new needs. Now, a little over a year since launch, Manometal’s stoked with the results.
“It was a challenging project, but thanks to the teamwork between everyone involved, we nailed the outcome both the client and we were aiming for.”
That’s from Matteo Ranuccini, Sales Manager at Trascar SpA.